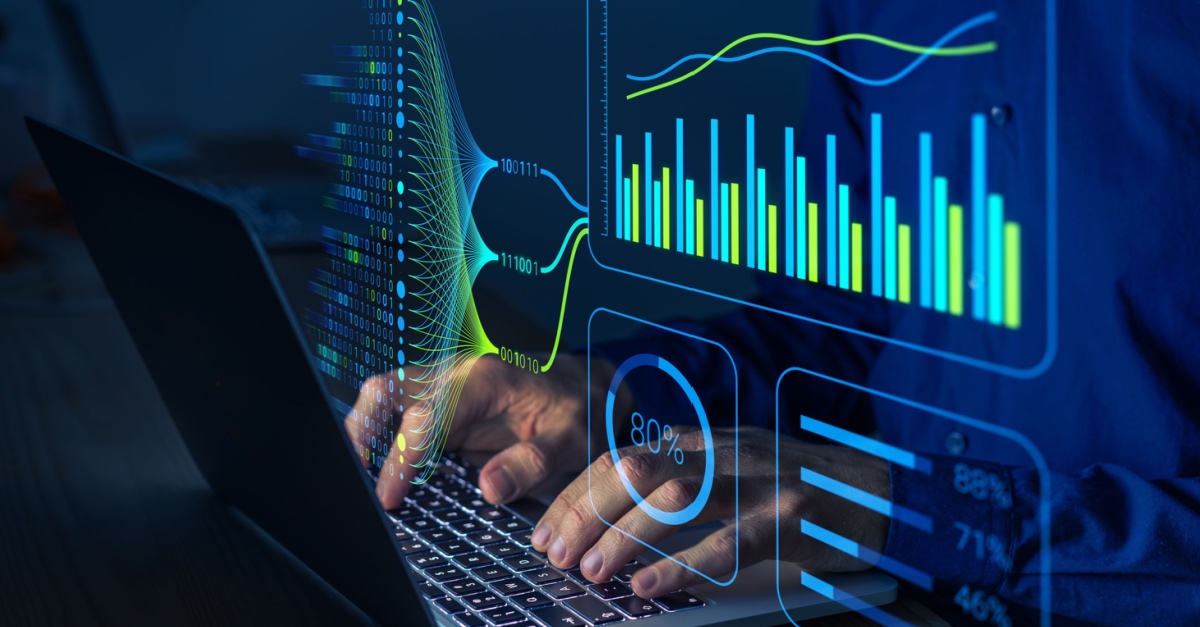
Transport operations the world over work hand-in-glove with manufacturing to power the world economy. Millions of tons of goods are moved daily by land (truck and train), sea, and air across vast distances to enable international trade and commerce.
The importance of data in transport operations cannot be overstated. It empowers companies to make better decisions, run more efficiently, send and receive shipments on time and (hopefully) reduce costs in the process.
Real-time data, in particular, plays a critical role in optimizing transportation operations. When run through analytical engines, it fuels up-to-the-minute insights into vehicle and container locations, traffic and weather conditions, and many other factors, enabling dynamic adjustments.
Data Provides Quantitative Insight into Complex Transportation Operations
Real-time data is defined as information that is delivered and processed immediately upon collection, allowing for quick decisions based on events as they happen. This type of data is particularly important in industries like global transport and logistics, where conditions affecting transit times are constantly changing.
Traditional data management relies on historical information from the prior day, week, month, quarter, or year. As such, companies employ various analytical methods to develop forecast models on which business decisions are based. Having access to real-time data significantly augments and enhances traditional data management, as it provides a view of actual conditions, activities, and transportation flows.
Tackling the Complexities of Managing Transport Operations
You may have heard that managing transport operations, especially those involving the movement of freight, is incredibly complex. And you would be right. Whether operating a private fleet, dedicated transport, or using third-party carriers, managing booking, routing, scheduling, loading, unloading, maintenance, etc., while keeping within budget is challenging.
Considering all these moving pieces, the high costs, and how business success relies on successful transport execution, the ability to access real-time data becomes that much more critical. Here are some of the key benefits.
- Enhanced decision-making: by leveraging real-time data analytics, transport operations managers have access to the latest information for faster, more accurate decision-making. From the ability to do dynamic routing and scheduling to load optimisation and asset utilization, there are all kinds of benefits that accrue.
- Improved operational efficiency: By enabling real-time tracking and monitoring of shipments, transport managers get instant visibility. Optimized routing and scheduling reduce fuel consumption and improves on-time delivery performance, lowering costs and improving service reliability.
- Increased visibility: Stakeholders such as shippers, customers and logistics partners can access up-to-the-minute information on transit times, ETAs, service disruptions, and performance vs. plan. This transparency improves customer satisfaction and aids in continuous improvement planning.
- Proactive issue management: Through early detection and alerting to potential disruptions, transportation managers can quickly enact contingency plans, setting in motion alternative routes and backup carriers to resolve issues before they escalate.
Real-Time Data in Action: How It Transforms Transport Operations
By leveraging real-time data, fleet managers go from being reactive and contending with potential gaps in information between reported vs. actual activity to being proactive and equipped with meaningful information that helps them improve performance.
Real-time data analytics is the fuel behind Tramm. An innovative transportation management system (TMS), Tramm’s suite features planning and route optimisation, transporter management, real-time visibility, and actionable business insights. It helps fleet managers elevate their operations internally and for customers.
Real-Time Vehicle Tracking and Status Updates
Tramm’s FleetVision module leverages real-time data from both onboard GPS and a proprietary driver app to continually track the location of every vehicle in the network. Users can also monitor how trips, loads, and shipment status are progressing vs. plan, get a live look at operational tempo, and automatically issue alerts on any plan deviations.
By monitoring every activity and status in real time, Tramm helps logistics and fleet managers make fast, informed decisions, adjusting routes to avoid delays while improving overall fleet efficiency.
Dynamic Route Optimisation
Tramm’s Route Optimization and Planning module dynamically adjusts routes based on its ability to monitor a range of factors. This allows for a continuous recalibration of delivery schedules and routes, making your transportation plan a model of efficiency and cost-effectiveness.
The system provides immediate feedback on things like running behind on a delivery window or a potential product-vehicle or vehicle-site mismatch. Managers are also notified in real time about vehicle utilization status. By continuously displaying these types of key insights, Tramm helps reduce fuel consumption, minimize delays, and optimize resource allocation.
Real-Time Performance Analytics
Tramm’s Dashboard module integrates real-time data analytics to offer comprehensive insights into network performance. Logistics and transportation managers can view live performance metrics, such as delivery times, operational flow, vehicle bunching, utilization rates, and schedule adherence.
Through powerful analytics, Tramm lets managers identify trends, pinpoint inefficiencies, and implement data-driven strategies to enhance operational performance. They are now empowered to respond swiftly, improving overall network reliability.
In Dynamic Transport Operations, Data Is the Differentiator
A hyper-connected supply chain, with shippers, carriers, freight forwarders, and fleet managers all dependent upon one another, needs real-time data to create a single source of operational truth. It is a true difference-maker, separating successful, highly efficient operations from those struggling to maintain SLAs and KPIs.
Each component of Tramm’s integrated TMS suite utilizes the power of real-time data to drive performance gains in managing transport operations:
- FleetVision Module: Provides live tracking of the planned vs. actual status on vehicles and loads, plus performance analysis, live predictive ETAs, and comprehensive exception management via a control tower view.
- Dashboard Module: A comprehensive data analytics/reporting tool that allows for analysis and data manipulation of the planned versus actual and historical data in the system to help you hit SLAs and drive continuous improvement.
- Mobile App: Provides real-time driver job assignments and updates plus ePOD (proof of delivery) and customizable operational workflow management on the go.
- Order Management: Rules-based order processing automates things like order splitting based on operational and resource requirements, designated delivery days and windows.
- Route Optimization: Handles complex routing scenarios and accounts for the details of each variable, like rules and constraints to accurately reflect actual operations.
- Transact: An easier way to manage loads, Transact allocates carriers based on preset rules and provides visibility into status, while automatically applying complex tariffs.
A Key Capability For Optimizing Transport Operations
Real-time data drives smarter, faster decision-making, improved efficiency, and greater supply chain visibility. It can help you stay competitive and address market challenges and disruptions as they arise.
Tramm’s innovative platform provides powerful capabilities that can transform your fleet operations into a leaner, more responsive, and performance-driven network. Request a demo today!
Related Resources
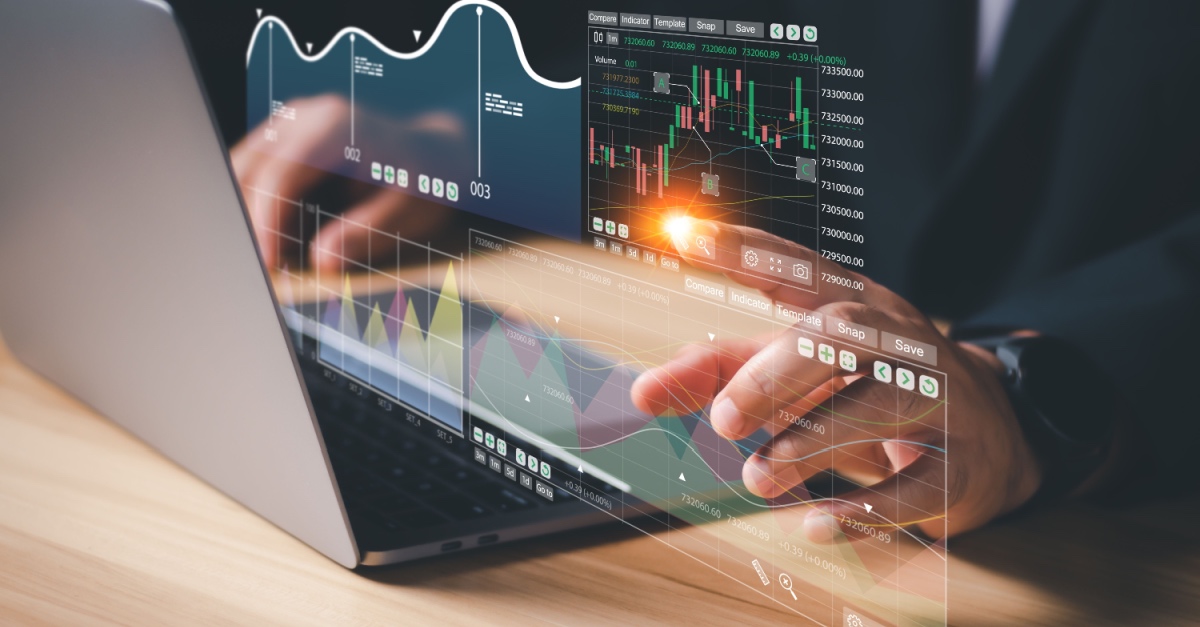
Smarter Shipping: Leveraging a Supply Chain TMS for Enhanced Business Intelligence
As we’re not yet living in the age of “Star Trek,” where people and things can be transported by breaking down and then reassembling molecules thousands of miles away (Elon Musk: take note), we here on Earth still count on shipping and logistics. By land, sea, and air, massive amounts of cargo are moved every day to keep global commerce humming. And a modern supply chain TMS (transportation management system) is a key technology that helps make it happen more efficiently.
Intelligent shipping combines business intelligence, planning, and execution tools, along with strategy and process, to optimize routing, scheduling, loading, communication, transporter management, etc. There are many primary and secondary benefits, including faster, more accurate deliveries, cost savings, improved customer satisfaction, better driver engagement and retention, and improved inventory management and demand forecasting.
A true supply chain TMS can help you achieve your goal of intelligent shipping by enhancing business intelligence and optimizing all aspects of logistics and transportation.
The Role of Supply Chain Analytics in Global Transport Operations
Supply chain analytics help organizations both keep track of and improve operational performance across various interdependent functions. All of that activity is throwing off tons of data, requiring sophisticated systems to synthesize and analyze, produce insights, and make recommendations. Increasingly, this is done by automating what had been manual processes, such as demand forecasting and route optimization.
The capabilities of supply chain data analytics have advanced significantly in recent years, increasing operational efficiency across all phases of transportation and logistics. For example, modern systems can assess risks associated with everything from geopolitical disruptions and natural disasters to freight capacity and supplier performance. Companies can then develop contingency plans and make better-informed decisions to mitigate these risks.
An advanced supply chain TMS can track KPIs such as the percentage of on-time deliveries, delivery error rate, cost per mile and cost per unit, load utilization percentage, average delivery time, and order cycle time. All of these metrics act as a barometer of business performance and efficiency.
Building Business Intelligence: Supply Chain Analytics Via a Powerful Supply Chain TMS
Tramm, an innovator in supply chain technology, has developed a platform based on the idea that a TMS can only be effective if every aspect of transport management is modeled, integrated, and visible from order inception to final delivery. The end-to-end Tramm TMS platform features route planning and optimization, transporter management, a supply chain control tower, and a powerful mobile app. Comprehensive reporting tools enable strategic planning, and performance analysis and performance management are enhanced via live tempo dashboards, trip scores, and more.
Tramm’s Dashboard Module provides powerful insights built from real-time, integrated external and internal data. Its control tower and visualization module, FleetVision, empowers managers to go from reactive (due to gaps between reported vs. actual performance) to proactive (based on live transportation data). With a better understanding of fleet operations on a granular level, loads are handled more efficiently, freeing up managers to implement performance improvement strategies.
A configurable Order Management module automates order processing, providing detailed visibility into order attributes. Integrated into Tramm TMS for seamless planning and execution, it automatically splits orders based on operational and resource requirements. A client portal allows end customers to capture, manage, and review order status.
Tramm centralizes all supply chain data, improving consistency and accuracy, eliminating discrepancies, and providing a single source of truth. Real-time updates and automated workflows further enhance data reliability, improving decision-making and overall supply chain efficiency.
Three Tactics to Build Business Intelligence through Supply Chain Analytics
To fully leverage the capabilities of a supply chain TMS and enhance business intelligence, companies need to implement specific tactics. Here are three tactics designed to help you achieve these goals, and how Tramm empowers you to do so.
Integrated Supply Chain Analytics
Supply chain analytics need to be woven into every aspect of transportation management. Tramm TMS centralizes data from multiple sources (orders, routes, transporters, etc.), ensuring that critical information is captured and processed in a unified manner.
Tramm eliminates data discrepancies and inconsistencies, creating a reliable, accurate foundation for all decision-making processes. It also provides a comprehensive view of the supply chain, enabling managers to make informed decisions quickly. In addition, internal and external teams have access to the same information, enhancing coordination and cooperation.
Real-Time Data and Insights
Tramm’s TMS and its real-time data processing capabilities allow transport managers to monitor and analyze activities as they happen. Continuous data updates provide a live view from order inception to final delivery, for improved route optimization, tracking, and inventory management.
This capability also allows for proactive identification of bottlenecks and inefficiencies, so managers can quickly implement corrective action and minimize disruptions.
Advanced Reporting and Visualization
Tramm’s supply chain TMS has powerful reporting and visualization tools that turn complex data into actionable insights, helping managers understand and act on key insights effectively.
The platform’s automated reporting on KPIs, such as delivery time, costs, and load utilization, surfaces performance trends and areas for improvement. Tramm’s Dashboard Module translates complex datasets into intuitive graphs, charts, and dashboards to aid decision-making.
Today’s Complex Logistics Call for a Supply Chain TMS That Does More Than Route Shipments
With global freight capacity tightening once again, a volatile market environment, and disruptions the norm, the limited functionality of a legacy TMS isn’t up to the task of managing complex functions across the supply chain.
Tramm TMS leverages the power of advanced analytics, real-time visibility, comprehensive reporting, business intelligence, and performance management tools. With it, organizations can get a better handle on transporter management, improving order flow, optimizing routing, and improving customer satisfaction. To learn how Tramm can transform your supply chain operations, request a demo today.
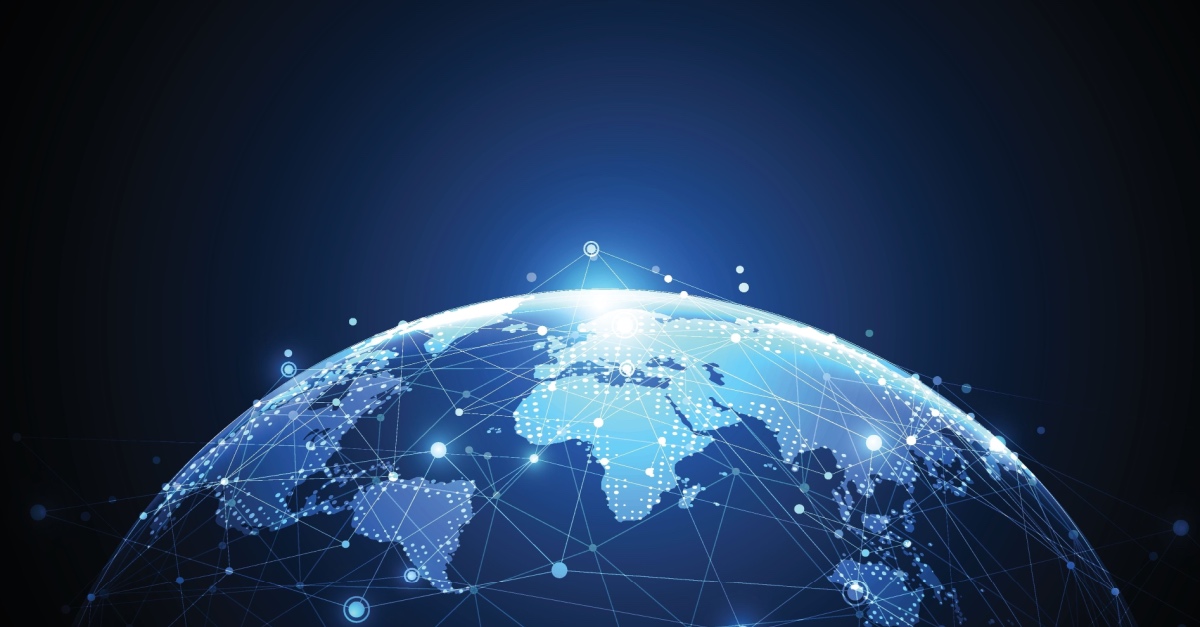
How Tramm TMS Enhances Communication Across the Supply Chain
Today’s highly interconnected supply chains are, in effect, massive networks that rely on all the players to do their part. Despite this, inadequate communication often results in lackluster coordination and is a primary chokepoint, leading to any number of failures. That’s why implementing a true supply chain TMS (transportation management system) is a key success factor.
TMS software is one way organizations look to create unified communication among supply chain stakeholders. Unfortunately, most systems today fail to achieve this objective, as they’re cumbersome, inflexible, and out of sync with interdependent pieces of the tech stack.
A lack of integrated communication and collaboration among external and internal supply chain partners ultimately frustrates customers and leads them to jump ship. Throw in all-too-common disruptions — tight capacity, port backups, geopolitical conflicts — and companies with poor supply chain visibility can’t give customers the kind of transparency they’ve come to expect.
This is where Tramm comes in. Tramm is a comprehensive TMS that is purpose-built to streamline supply chain operations within a unified platform approach. By integrating communication, route optimization, order management, and a control tower for real-time visibility, Tramm ups efficiency, reduces costs, and helps improve CSAT scores. All of this addresses critical pain points felt today across logistics management.
In this article, we’ll explore the issues and limitations of TMS systems and how Tramm addresses them by enhancing communication across the supply chain. We’ll unpack how Tramm is built on a simple yet rarely implemented idea: a TMS can only be effective if every aspect of transport management is modeled, integrated, and visible from order inception to final delivery.
Communication: A Key Chokepoint for Complex Supply Chains
In logistics, every operational execution — whether store delivery, inbound DC shipment, or DTC order — touches multiple functional areas: transportation, order management, customer data, and warehouse management. Without a unified communication approach, things can break down quickly, as we’ll illustrate with this hypothetical scenario:
Jessica orders a dress for a friend’s wedding that's four days away, choosing the retailer’s two-day delivery. The OMS confirms her purchase, but an inventory system error shows it as in stock at a nearby store for e-commerce fulfillment when, in reality, it’s sold out. The next day, the same dress is located at a warehouse 500 miles away, and the order is re-routed, adding a day in transit.
Three days after the order was placed, it’s out for delivery, but the truck breaks down on the way. Due to poor fleet visibility, a delivery status update isn’t communicated to Jessica. On top of that, an address change she entered on the e-commerce website goes into the CRM, but this data isn’t synced with the TMS. So, a driver leaves the package at her old address. Jessica, anxiously trying to track her order, contacts customer service, but a lack of synchronization between systems leaves her without answers. The dress finally arrives — a day after the wedding — and a high-value customer is lost.
This unhappy ending demonstrates how vital seamless communication is, given the intricate nature of today's supply chains, where even a minor failure has financial repercussions. Think, for example, of the high cost of customer acquisition vs. retention.
We’ll now look at three specific challenges of supply chain communication faced by organizations today.
Fragmented Systems
Fragmented systems create significant barriers to effective communication. This disconnection leads to the creation of information silos across disparate systems, making it hard for each operations team to access accurate, consistent data. Poor integration hampers their ability to coordinate assets and tasks, increases the likelihood of errors, and reduces operational efficiency.
Inconsistent Data
Inconsistent data poses a major supply chain challenge, as variations in formats and sources lead to bad information and worse decisions. This undermines the reliability of communication, causing confusion and errors. Ultimately, it hampers your ability to coordinate effectively with other functional teams, limiting efficiency and dinging customer satisfaction.
Manual Processes
Manual processes increase the risk of errors and slow down the flow of crucial information. Depending on paper-based methods often causes delays and makes it difficult to maintain accurate, timely communication. This ultimately impacts decision-making and results in poor operational performance.
To quote Strother Martin to Paul Newman as the cruel prison captain in “Cool Hand Luke”: “What we’ve got here is … failure to communicate.” Updates from manual processes, sometimes using Excel sheets, is a recipe for disaster, especially considering the need for real-time data sharing between systems, internal teams, carriers, 3PLs, and customers.
Integrated Communications: Revolutionizing Coordination with Supply Chain TMS
Tramm has developed an innovative TMS solution that integrates supply chain communications in a single powerful, intuitive platform. It ties together order management, route optimization, planning and scheduling, carrier management, a control tower for shipment visibility, and a mobile app with customizable workflows and electronic proof of delivery (ePOD) for driver management.
A true supply chain TMS, Tramm offers broad optimization across many aspects of logistics operations, from order processing to delivery, carrier billing, returns, and exception management. The results are greater efficiency, reduced costs, improved performance (order accuracy, on-time delivery, etc.), and enhanced customer satisfaction.
Tramm’s configurable solution has many automation capabilities for a variety of supply chain functions, including alerts for off-plan events, automated reporting, driver debriefing, and communication via standard tools (WhatsApp, email, SMS) with customers, drivers, and managers.
Here are more details on different aspects of Tramm TMS and what sets it apart from traditional solutions.
Platform Unification
Tramm TMS addresses the problem of fragmented supply chain systems by integrating key functions into a unified, scalable platform. It centralizes data, ensuring consistency, accuracy, and integrated communication. The FleetVision control tower provides real-time visibility into vehicle location and ETAs, route adherence, and load status.
Transportation managers can set up customized, automated workflows to manage drivers and routes via the Tramm mobile app. For instance, it can include detailed instructions such as the level of signature required for each stop, when to scan a code, if a confirmation picture is required, etc.
Information from the app is fed back into the Tramm system for planning, reporting, and performance management purposes. For instance, location data from the driver’s device is compared to the onboard GPS to identify any errors or inconsistencies.
Seamless Data Integration
Tramm TMS centralizes all supply chain data in an accessible, intuitive platform with mobile access. This ensures data consistency and accuracy, eliminates discrepancies, and provides organizations with a single source of truth. Real-time updates and automated workflows further enhance data reliability, improving decision-making and overall supply chain efficiency.
Data usability and accessibility are some of the main benefits. Team members across supply chain functions get access to precise data and analytical insights for improved performance monitoring, planning, and reporting.
Tramm’s platform brings in data from internal as well as external partners (carriers, brokers, freight forwarders, 3PLs, etc.) via APIs. Drivers, managers, planners, and executives all get a unified view via the app to real-time tracking and status information, hours of service remaining, precise delivery locations and pickup requirements, KPIs, and much more.
Automated Supply Chain Accuracy
Tramm TMS alleviates cumbersome manual processes by automating key workflows to reduce reliance on manual data entry and paper-based methods. It streamlines operations with dynamic updates, integrated communication tools, and centralized data management.
Tramm’s rules-based order processing automates things like order splitting based on operational and resource requirements, as well as designated delivery days and windows for end customers, with the option of manual intervention where necessary. Tramm’s dashboard includes automated reporting, analytics, and business intelligence capabilities. This empowers decision-makers with a clear understanding of operations, performance, and growth opportunities.
Jessica’s Story, Reimagined
Now, let’s return to our earlier example of the fictional Jessica and her ill-fated dress order, with Tramm as the hero of the story.
Jessica orders her dress, and Tramm’s OMS confirms her purchase, pulling directly from the retailer’s inventory management system to confirm it’s in stock. Tramm also selects the optimal carrier and delivery window based on the customer’s location and the retailer’s requirements, handing this information off to the TMS for dispatch.
On the promised date, the driver, using the Tramm mobile app, notes Jessica’s delivery preference (side door). The ePOD function notifies the system of a successful dropoff for performance monitoring and reporting. Jessica, meanwhile, having received regular notifications of the order in transit at every scan, is thrilled with the experience (and the dress). She has a blast at the wedding, and the retailer gets a smiley rating from their happy customer.
Yesterday’s TMS Can’t Handle Today’s Exacting Supply Chain Communication Needs
How is it possible to have an optimized, efficient supply chain when internal and external data is siloed, and stakeholder communication sometimes feels like today’s equivalent of cans and strings? Answer: it’s not possible.
This leads to all kinds of negative downstream effects: missed opportunities, time-consuming manual processes to cover system gaps, inadequate reporting, and business intelligence insights, poor visibility into assets and deliveries, increased costs, and dissatisfied customers.
Tramm’s unified suite enables shippers, 3PLs, carriers, and their partners to accurately communicate the intricacies of day-to-day supply chain operations. Through our powerful app, control tower visibility, customizable dashboard, and precision planning capabilities, companies can increase efficiency and optimize execution. Analytics and reporting, including KPI-based internal and external scoring, lead to smarter decisions and better outcomes for customers and businesses.
To learn more about how Tramm can make a difference by unifying your supply chain communications, request a demo today.
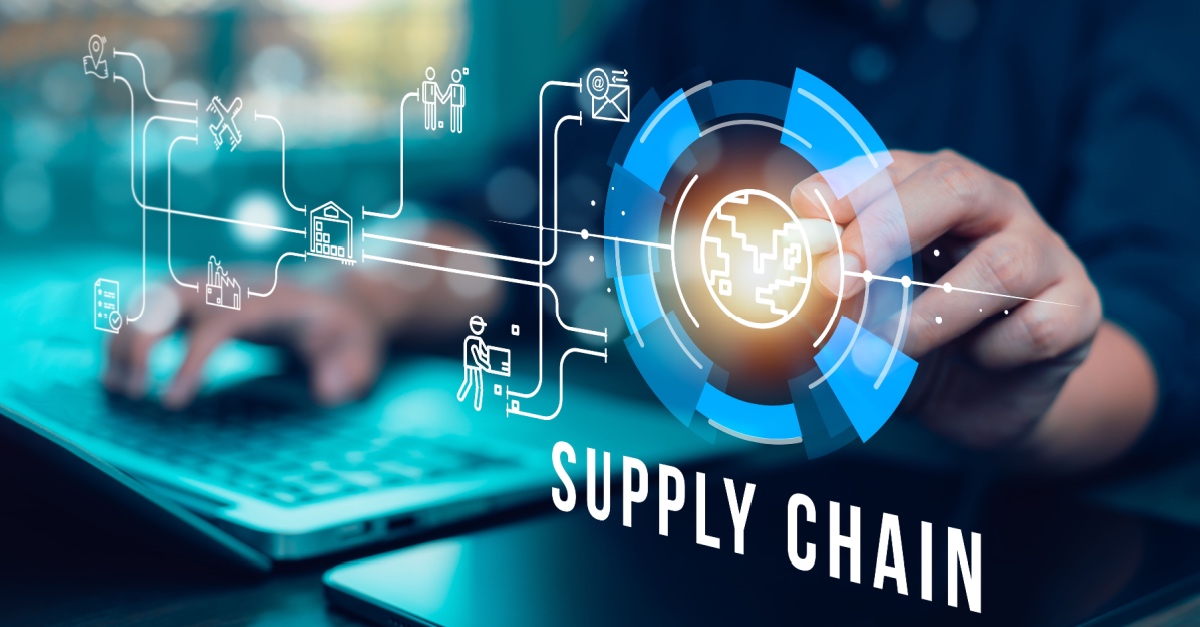
Synchronized Logistics: Leveraging An Integrated TMS for Real-Time Supply Chain Management
An integrated supply chain TMS helps make tight partner collaboration and data collection from multiple sources possible so goods flow smoothly, SLAs are hit, and production stays on track.
It’s also a key element in synchronized logistics, a process that businesses lean on to manage multiple complex systems. This involves pulling together and analyzing data from disparate sources, all of which touch the supply chain in some way: transportation management systems (TMS), warehouse management systems (WMS), enterprise resource planning (ERP), and even yard management systems (YMS). Using data analytics, synchronized logistics pulls together insights that can then be applied to various supply chain processes.
In this context, an integrated supply chain TMS can achieve synchronized logistics by enhancing business intelligence and optimizing all aspects of transportation. This, of course, has multiple benefits up and down the supply chain, such as faster inventory turns, better delivery metrics, and improved asset utilization, among others.
An integrated TMS uses advanced business intelligence to optimize logistics and transportation by analyzing large sets of real-time and historical data. It helps identify patterns and inefficiencies, predict delays, and recommend optimal routes. Using predictive analytics to forecast demand can optimize capacity utilization and automate decision-making, such as selecting the most cost-effective carriers or adjusting delivery schedules.
An integrated TMS enables more precise planning, cost control, and supply chain efficiency by incorporating data from ERP, WMSs, and other systems. This helps companies improve planning and execution, reduce delays, and respond quickly to disruptions. Using AI-powered data analytics, businesses can fine-tune their operations and keep costs in check.
As the need for real-time supply chain visibility grows, the role of an integrated supply chain TMS becomes even more critical. Its ability to synchronize logistics and provide actionable insights helps companies stay competitive in an increasingly dynamic market.
What is an Integrated TMS in the Supply Chain?
An integrated TMS is a comprehensive platform designed to streamline the core functions of supply chain management: planning, execution, and optimization of transportation activities. It helps businesses plan efficient routes, execute shipments, and optimize delivery schedules to reduce costs and improve performance.
It also helps meet heightened performance expectations by providing visibility and agility across the supply chain. Unlike a traditional TMS with limited connectivity, an integrated TMS hooks into multiple complementary software systems. Creating a cohesive information flow across the supply chain enables more informed decision-making and better cross-functional collaboration. Businesses benefit from real-time tracking, updates, and greater visibility into logistics operations.
The Importance of Real-Time Supply Chain Management
Customers in both B2B and B2C are demanding faster delivery times, more accurate ETAs, tight delivery windows, and real-time updates on order status. Call it the “Amazon effect,” driven by the higher service level expectations created by the mega e-commerce company turned logistics powerhouse. Especially in a tighter economy, there is little margin for error in terms of costs, the balance sheet, and customer churn.
Real-time supply chain management involves continuously monitoring and managing supply chain activities as they happen. This is where synchronized logistics comes into the picture. Real-time data from integrated systems provides immediate visibility into inventory, shipment status, and fulfillment operations. This allows businesses to make quick, informed decisions, optimize routes, and adjust to changing conditions. The result is increased efficiency, cost savings, and improved customer service.
Key benefits of real-time supply chain management include:
Quick response to disruptions: Real-time supply chain management enables businesses to respond swiftly to issues like traffic, port congestion, or weather delays. With immediate access to updated data, they can quickly adjust routes, reschedule shipments, and notify customers, minimizing delays and maintaining operational efficiency.
Optimized route planning: Real-time data from TMSs allows businesses to dynamically optimize routes based on current conditions such as traffic or road closures. This reduces transit times, improves fuel efficiency, and enhances on-time delivery rates, leading to cost savings and improved KPIs.
Improved customer satisfaction: Accurate real-time tracking ensures customers receive up-to-date information on shipment status, including greater accuracy in delivery estimates. This transparency and proactive communication build trust and loyalty by enhancing customer experience (CX), helping companies exceed delivery expectations, and improving customer satisfaction.
Core Features of an Integrated TMS That Supports Synchronized Logistics
An integrated supply chain TMS offers a wide array of features designed to improve supply chain management and logistics flow:
Real-Time Tracking and Visibility
A supply chain TMS allows you to monitor each shipment from order to delivery by providing continuous updates on shipment location, inventory status, and delivery progress. This level of transparency allows you to quickly address potential issues (delays, misrouting, breakdowns) before they escalate. The system’s ability to provide real-time views into supply chain flow improves accountability and efficiency.
Advanced Data Analytics
Integrated TMS platforms use predictive analytics to anticipate delays, optimize routes, and improve decision-making. Predictive and even prescriptive insights allow businesses to proactively avoid disruptions and refine logistics strategy.
Automation and Collaboration
Automation tools facilitate freight scheduling, real-time communication with carriers, and stakeholder collaboration. This reduces manual intervention and enables teams to focus on higher-value tasks.
Seamless Integration
An integrated TMS connects with other systems to synchronize supply chain operations. This ensures data flows smoothly between departments, teams, and partners, helping streamline processes and reduce delays.
Overcoming Common Supply Chain Challenges with Integrated TMS
An integrated TMS helps businesses address several common supply chain challenges:
Reducing delays and inefficiencies: Real-time updates allow companies to anticipate and avoid delays. With real-time visibility, businesses can reroute shipments or adjust schedules to minimize disruptions.
Improving demand forecasting and inventory management: Data generated by a TMS helps logistics planners maintain lean inventories while still meeting customer demand. With accurate, up-to-date information on shipment status and inventory levels, they can more closely align supply with demand, reducing the risk of stockouts or overstocking.
Adapting to market changes: Market volatility and changes in consumer behavior can disrupt supply chains. An integrated TMS helps businesses become agile through real-time adjustments to routes, carriers, or schedules in response to changing conditions.
The Role of Data in Synchronized Logistics
Data is the backbone of synchronized logistics. An integrated TMS collects, processes, and analyzes vast amounts of data to drive more informed decision-making.
A TMS provides real-time data, enabling better decision-making in procurement, route optimization, and warehouse management. Accurate, timely information helps businesses be more proactive and improve overall efficiency.
Many advanced TMS platforms incorporate AI and machine learning algorithms to predict risks, optimize freight rates, and automate repetitive tasks. These technologies enhance the system’s ability to make real-time adjustments, delivering improved operational efficiency and reduced costs.
By leveraging real-time data, businesses can provide more accurate information to customers about shipment status, improving transparency and loyalty. Data-driven synchronized logistics enhances CX by ensuring timely deliveries and proactive communication.
Choosing the Right Integrated TMS for Your Business
Some attributes of an integrated TMS include its intuitive UI, which makes it easy for nontechnical users to manage both owned and contracted transportation assets. This includes streamlining aspects of transportation management, such as contracts and payments.
Scalability is another important feature, as well as a cloud architecture and ease of integration with other systems through API connections. A supply chain TMS should also be customizable and rules-based, adaptable to prioritize the execution of last-mile delivery, international shipping, or retail replenishment. Mobile workflows, master data attributes, exception management, self-reporting, and business intelligence should all be easily configurable based on your business needs.
The importance of provider reliability cannot be overstated. Look for a company that offers robust customer support, ongoing training, and regular system updates to address evolving industry and business needs. This is a recipe for long-term success, giving you the ability to maximize system capabilities.
An Integrated TMS: Creating the Future of Supply Chain Efficiency
An integrated supply chain TMS plays a pivotal role in powering synchronized logistics so businesses can streamline operations and respond in real time to supply chain challenges. Consolidating data from multiple systems enhances visibility, optimizes routes, and minimizes disruptions. Companies can make informed decisions, improve delivery performance, and reduce costs through advanced analytics and automation. These next-generation systems ensure a more agile, efficient, and customer-centric supply chain.
Tramm TMS is the first SaaS platform using advanced technology to enable companies to easily manage all transportation assets, both owned and third-party, from the first mile to the last mile.
It is purpose-built to streamline supply chain operations, synching data to create a single source of truth. By eliminating data silos and tapping the power of AI-driven insights, Tramm streamlines processes and ensures a consistency of action across the supply chain.
With its modular, scalable architecture, Tramm’s solution set includes an order management system (OMS), a visibility and control tower module, a global transporter module, a dashboards module, and a driver app. Its platform marries flexibility with optimization, powering a customer-centric approach that delivers measurable results. To learn more about Tramm’s ability to power synchronized logistics and increase supply chain efficiency in your organization, request a demo today.
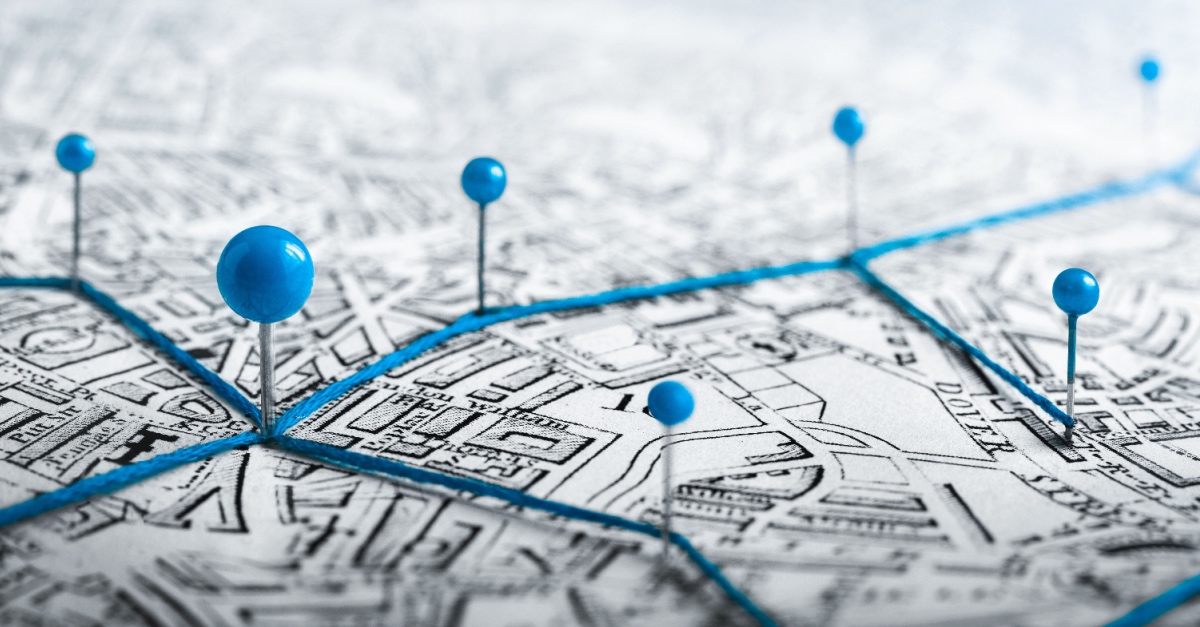
Route Optimization: The Key to Effective Logistics Planning
Listen to any quarterly earnings call from major logistics services firms like UPS and FedEx, and you’re bound to hear a plethora of statistics that deal with delivery performance: average miles per delivery stop, stops per route, packages per driver hour, cost per package, on-time delivery rate, etc.
These figures matter a great deal because they help determine the company’s profitability (or loss) that quarter, as indicators of operating performance expressed in KPIs. They also have a great deal to do with the concept of route optimization, the art and science of executing deliveries as efficiently as possible.
Within the broader scope of logistics planning – coordinating the movement, storage, and flow of goods within a supply chain – route optimization plays a key role. Transportation managers put a great deal of effort into reducing total miles, eliminating delays, and improving route density metrics (number of stops, packages per stop, per driver, etc.). Performance goals include higher on-time rates, lower operating costs, and higher customer satisfaction, among other key business objectives.
We’ll take a closer look at route optimization, why it matters, how it’s achieved, and the technology behind it.
Aspects of Route Optimization
In logistics and transportation, whether truckloads from a plant to a distribution center or stepvans from a hub to a local run, route optimization involves finding the most efficient travel paths. Factors include the distance between points, traffic patterns, delivery windows, fuel costs, and vehicle capacity.
Determining the best fleet to use in each case is also an important success factor. Transportation managers must not only select between different vehicle types and sizes for each set of deliveries, but also the right number of each type based on fixed and variable costs. Fixed costs include driver salaries and wages, vehicle leasing or depreciation, insurance, licensing and permits, and administrative costs. Variable costs include fuel, driver overtime, maintenance and repairs, tolls, loading and unloading, and third-party fees when using a logistics provider.
In addition to vehicle type and size, other route optimization variables include product suitability and restrictions (i.e., refrigerated), road networks, customer time windows, backhaul opportunities, driver hours of service (HOS), efficient load building, and fuel/rest stop planning.
Balancing fixed and variable costs is important because it helps achieve route optimization by minimizing the total cost per delivery while maintaining efficiency and delivery schedules. By selecting the right number of vehicles, adjusting for stop density, and optimizing distances, businesses can achieve substantial savings and performance gains.
Why Route Optimization is Crucial
Through route optimization businesses can achieve greater cost efficiency, improve delivery performance, and foster sustainability. By identifying the most efficient travel routes, they can minimize fuel consumption, lower labor costs, and reduce vehicle wear and tear. This is particularly important in a competitive environment where even small cost savings can spell the difference between a division’s profit and loss.
Optimized routing helps ensure timely deliveries, improving service reliability and customer satisfaction. From an environmental perspective, it means reduced fuel usage and lower carbon emissions, supporting sustainability initiatives and regulatory compliance. This is also something that can resonate with customers who value greener transportation.
Route optimization also helps companies maximize resource utilization through increased efficiency of vehicle, driver, and asset usage. By balancing fleet capacity, stop density, and delivery schedules, transportation managers can reduce empty miles and truck idling. The result: more streamlined operations, better use of resources, and improved performance.
Logistics Challenges Affecting Route Optimization
It’s hard to believe given technological advances across logistics functions, but manual route planning is still widespread, especially among small to mid-sized businesses. Many companies continue to rely on a combination of spreadsheets, paper maps, or simple routing tools for delivery and route planning. These methods are often in use when delivery volume is manageable and the network is relatively small. But they are inefficient, lack scalability, increase costs and risk customer dissatisfaction.
As supply chains become more complex and expectations increase, the use of route optimization software is growing. Advanced tools like transportation management systems (TMS), GPS tools, and AI are becoming much more common. They all leverage real-time data, machine learning and predictive analytics to optimize routes based on factors such as traffic, weather, fuel costs, and delivery windows.
Larger enterprises – both logistics providers and shippers – rely heavily on advanced route optimization technology to manage vast delivery networks. As e-commerce growth and customer expectations rise, more companies are shifting toward automated solutions to stay competitive and improve operational efficiency.
The Role of Technology
Technology has revolutionized route optimization, enabling businesses to streamline logistics and reduce costs. Route optimization software integrates GPS, telematics, and algorithms, analyzing real-time and historical data to create the most efficient travel paths. These tools consider variables like traffic patterns, weather, delivery time windows, and vehicle capacity.
AI and machine learning enhance these capabilities with predictive analytics, looking at traffic trends, fuel costs, and customer demand to anticipate delays and proactively recommend adjustments. Machine learning models continuously refine routing strategies by analyzing historical data, improving accuracy and adaptability.
By integrating these technologies into logistics planning, companies can reduce total miles driven, minimize delays, and optimize resource use. This helps them achieve their key goals (cost savings, higher on-time delivery rates, improved customer satisfaction).
Key Features of Route Optimization Software
Route optimization software gives logistics managers an advanced tool for improving efficiency and reducing costs. A key feature is vehicle selection. When the optimal vehicle is chosen for each route based on capacity, cost, and suitability, it maximizes utilization and reduces costs. Dynamic route adjustments allow for real-time updates based on changing traffic, weather conditions, or unexpected delays, helping maintain on-time performance.
Multi-stop optimization efficiently sequences stops for deliveries, reducing total miles driven and improving route density. Beyond basic stop sequencing, route optimization software should be designed to handle the complexity, nuances and business rules of each company. This could include factoring things like load building based on relative item weight, customer delivery windows, and site restrictions, to optimize stop sequencing.
System integration ensures seamless communication with WMS, TMS, and fleet management systems (FMS), providing end-to-end visibility across functional areas. And driver behavior analytics enhance efficiency and safety by monitoring factors such as speed, braking patterns, and fuel consumption.
Best Practices for Implementation
Successfully implementing route optimization software requires a strategic approach. Start by defining clear objectives that align with your business goals. This includes identifying key metrics such as cost savings, delivery speed, or carbon emissions reduction in order to measure success effectively.
Invest in scalable technology that can grow with your business. As you expand or deal with demand spikes, the solution should be able to adapt to meet changing demands without disrupting workflows.
Provide thorough training in order to maximize the benefits of routing tools. A well-trained workforce leads to better decision-making and greater efficiency.
Prioritize continuous monitoring and adjustment. Real-time analytics can identify inefficiencies, respond to changing conditions, and fine-tune processes. Regular reviews ensure the system continues to deliver value over time and adapts to evolving challenges.
Partnering with the Right Technology Provider
Key characteristics to look for include proven expertise in logistics software and analytics, as well as an understanding of your industry's specific needs. Scalability is another important requirement, future-proofing the technology so it can grow with your business and adapt to changing needs. The ability to provide seamless integration via API or EDI with WMS, TMS, and FMS sets up real-time data sharing and better collaboration across the supply chain.
The right provider should be able to deliver a realistic implementation timeline that factors in data readiness, integration complexity, user training and any customization. For SMBs with fewer requirements, it can happen in a matter of weeks; in more complex enterprise scenarios it can take 3-6 months, often in a phased rollout.
Continuous updates ensure the technology stays on track with advances in AI, machine learning, and predictive analytics. The provider should also be able to deliver a tailored solution that addresses your unique requirements. This will help optimize performance, increase efficiency and cost savings, and improve delivery speed and accuracy, delighting customers and building loyalty.
A Tech-Driven Route To Greater Transport Efficiency
Route optimization has become a cornerstone of supply chain management, and a reliance on outdated manual processes falls woefully short of achieving its goals. Through advanced technology, businesses can become more efficient, save on costs, and improve customer satisfaction and sustainability.
Tramm, an innovator in supply chain technology, has developed a cloud-based end-to-end TMS platform that combines route planning and load building, transporter management, order management, a logistics control tower, and a mobile app. With this approach, Tramm has solved the problem of fragmented supply chain systems, integrating key functions into a unified, scalable system.
Tramm’s Planning and Optimization Module leverages powerful algorithms to handle complex routing environments, accounting for variables that accurately reflect on-the-ground transport operations. Its dynamic multi-day route planning handles scheduling for primary, secondary, and service-based fleets. Users can easily make real-time adjustments based on changing needs, including “what if” visualization and scenarios. A load builder/stackability app automatically plans loads that are tightly synced with capacity and route optimization.
To find out how Tramm’s unified approach can drive transportation efficiency and cost savings while helping you realize sustainability goals, request a demo today.
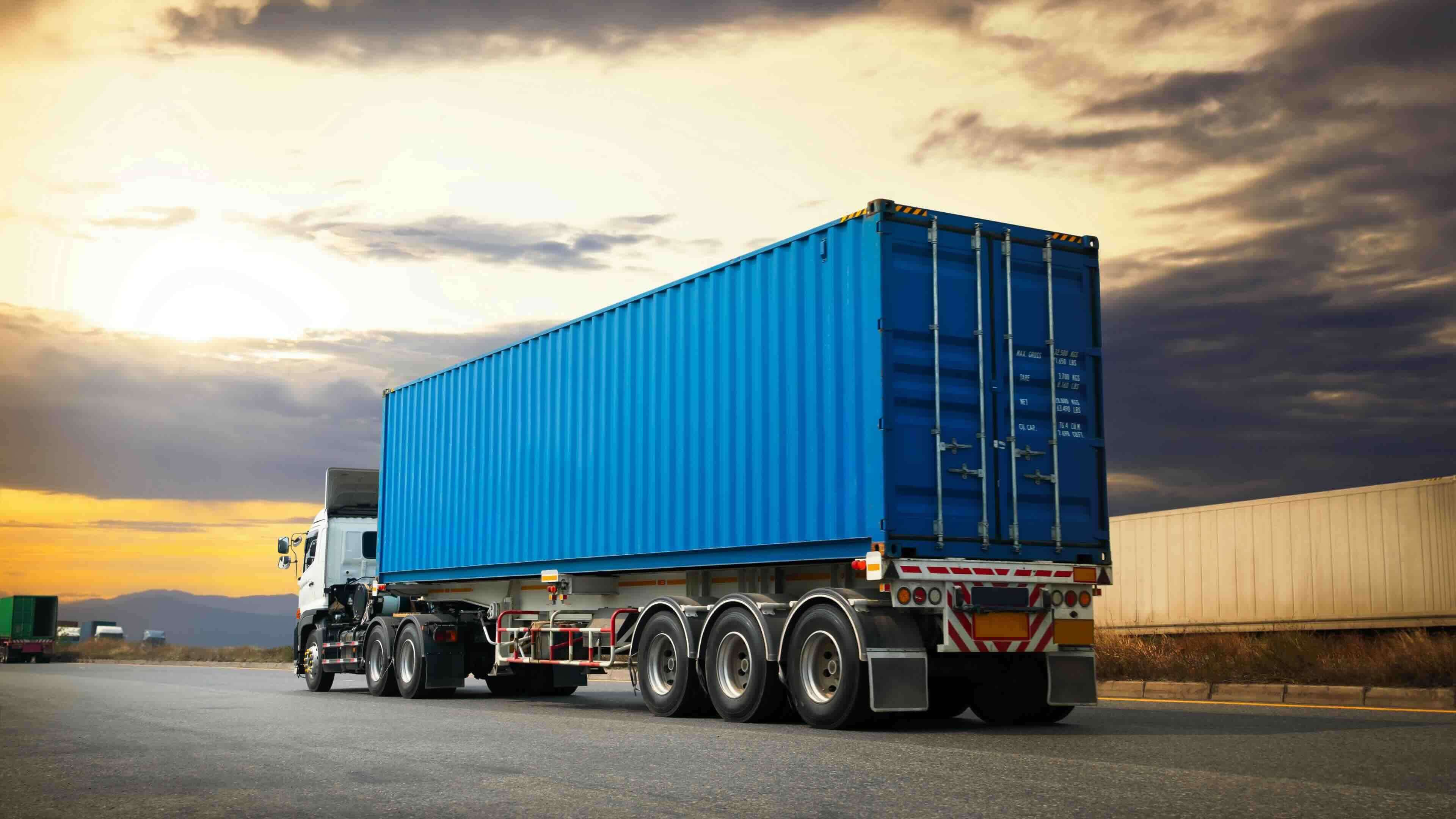